Coal Pulverizer are designed to reduce the size of the incoming raw coal to a fineness that will result in good furnace performance. The grinding surface in the pulverizer resembles a shallow dish or bowl. Therefore the name “Bowl Mill” has been adopted to refer to this piece of equipment.
Components of Bowl Mill Coal Pulverizer
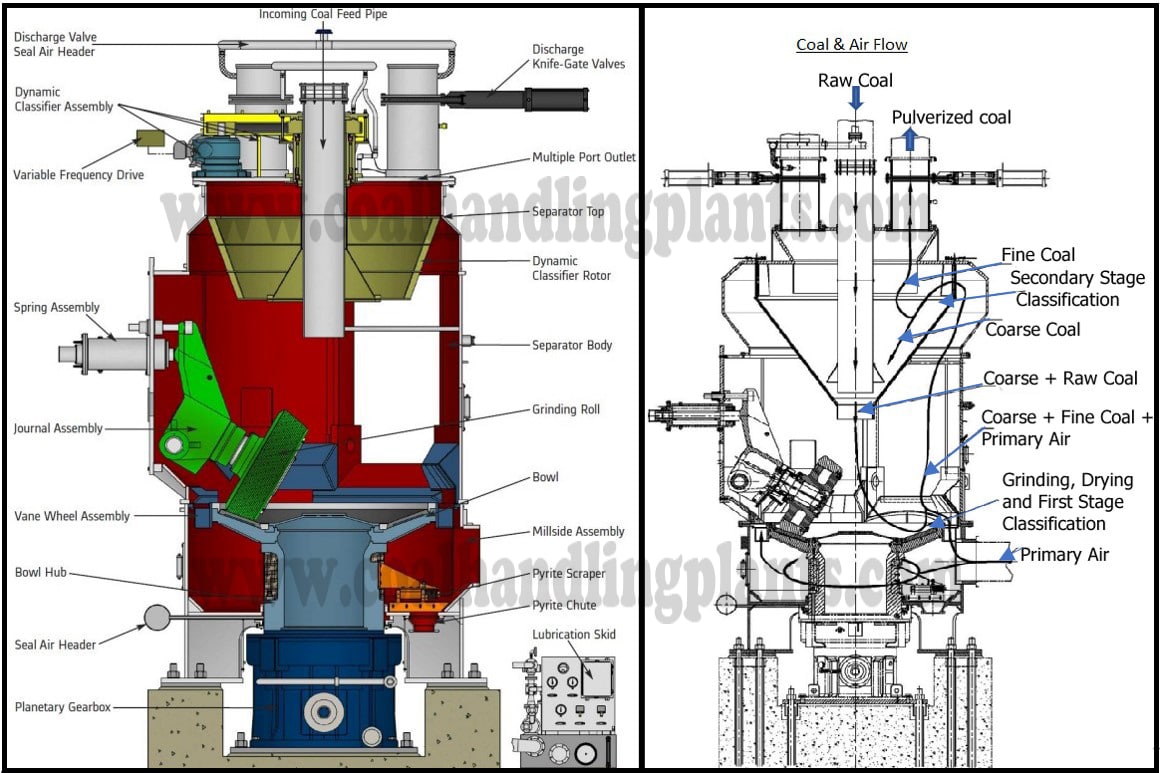
Gearbox
It is driven by an electric motor, is directly connected to the bowl hub. A planetary gear arrangement provides the proper reduction between the motor and the bowl hub to obtain the desired bowl speed.
Millside and air inlet
It surround the bowl and the bowl hub and support the separator body. Air for transporting and drying the coal enters through the air inlet and is directed upward around the bowl.
Bowl
It is the table upon which the coal is crushed. Material to be ground is admitted to the coal pulverizer and deposited near the center of the rotating bowl.
Vane Wheel Assembly
It is attached to the bowl, directs the coal/air mixture within the grinding zone of the pulverizer by uniformly distributing the transport air through the bowl OD and separator body annulus.
Journal Assemblies
Three independent, spring loaded “journal assemblies” are suspended from the separator body and overhang the bowl. The journal assembly rolls are free to rotate, and do so, when the coal being pulverized fills the space between the rolls and the bowl.
Separator Body and Separator Top
It contain the material after it is pulverized. The separator body and separator top direct the material and transport air up to the static classifier.
Static Classifier
It separates the coarse coal particles from the fine ones and returns them to the bowl for further grinding. Fine coal is discharged through the coal piping to the coal nozzles at the furnace.
Working of Coal Pulverizer
The maximum capacity of a pulverizer is dependent on the following:
1. Pulverizer size
2. Raw coal properties – Hardgrove index and moisture level
3. Pulverized coal fineness
The raw coal is fed into a rotating bowl via a center feed pipe. The rate of coal feed is normally determined automatically by a combustion control system, taking into account the MW demand on the unit, coal quality, and the number of coal pulverizers in service. Centrifugal force causes the coal in the bowl to move radially outward, building up a bed of coal on the grinding ring.
The bed of coal passes under pivoted grinding assemblies called journals. Here, spring produced loads are imparted to the coal by the rotating rolls. Size reduction takes place in the localized area between the grinding ring (called the bull ring) and journal roll through crushing and a process know as attrition or friction grinding.
The radial and circumferential movement of the coal carries the pulverized coal up over the edge of the bowl into the path of the hot air stream. The hot air supplied to the pulverizer has two primary functions:
1. The hot air dries the coal.
2. The hot air is used for transportation of the recirculating coal within the mill and also for
transporting the coal from the pulverizer to the furnace.
As the coal is continuously reduced in size, the smaller/lighter particles are swept from the bowl by the hot air. Hot air (and cool tempering air) is provided by the primary air fans. The air is admitted below the pulverizer bowl into an area known as the millside and air inlet. The millside is at a positive pressure.
From the millside, the air flows upward around the outside diameter of the rotating bowl. Vanes attached to the bowl (vane wheel) change the airflow to a vertical direction. At the edge of the bowl, smaller/lighter particles of coal are entrained in the air stream and are carried upward, while dense, difficult-to-grind foreign material is rejected downward through the air stream into the millside.
Above the bowl, the lighter airborne coal particles undergo a two-stage classification process:
1. The first stage of classification takes place just above bowl level. Stationary air deflectors mounted on the separator body cause the heaviest coal particles to abruptly change direction, they loose momentum and are returned directly to the bowl for further size reduction.
2. The lighter particles are carried by the rising air stream up to the separator top where they enter the static classifier. Here, the torturous path causes the fine particles to be separated from the coarse particles. The fine particles exit the mill thru the fuel pipes and the coarse particles are returned to the bowl thru the inner cone for further size reduction.
At the coal pulverizer exit, the coal-air stream is distributed directly to the coal pipes. The difficult-to-grind foreign material which falls through the air stream into the millside is moved by rotating scraper assemblies, to an opening in the millside floor. The rejected foreign material falls out of the coal pulverizer and enters the pyrite system. The rejected material usually consists of rock found as over or under burden in the coal seam and/or other ungrindable material entering with the raw coal feed.
Improper Coal Pulverizer Operation
Listed below are incorrect and hazardous operating conditions which should be avoided.
1. Excessive coal spillage is a hazardous situation which can plug the pyrites discharge chute thus allowing a coal buildup in the millside and increasing the potential for a pulverizer fire.
2. Operating a coal pulverizer for an extended period of time with outlet temperature below specification is hazardous since the coal may not be properly dried and will plate out inside the coal pulverizer and in the fuel piping. Fuel pipe plugging and pulverizer or fuel pipe fires can result.
3. Operating a pulverizer with the outlet temperature above specification is hazardous because high outlet temperatures can drive volatile gases from the fuel thus increasing the fuel’s potential to ignite. The control system should automatically close the hot air shutoff gate if the pulverizer outlet temperature rises to 11°C (20°F) above the specified normal outlet temperature.
4. Operating a pulverizer with reduced airflow (below specification) is hazardous since velocity in the fuel pipes may not be adequate to maintain the pulverized coal in suspension. If coal settles it can cause fuel pipe plugging and fires.
5. Operating a pulverizer with airflow above specification is considered less then optimal; the higher airflow will increase internal wear in the fuel pipe and pulverizer. It can also cause a reduction in the pulverized coal fineness.
6. Operating a pulverizer with the pyrite discharge gate closed is prohibited because it prevents the normal discharge of rejects. When the gate is closed for extended periods of time, material normally discharged will be retained in the millside. The scraper assemblies can be severely damaged and the potential for a pulverizer fire is increased.
7. Operating a pulverizer with one or more coal discharge valves not fully open is considered hazardous since it will increase the pulverizer pressure drop, adversely affect coal fineness and cause an unbalance to the coal pipe distribution which could result in coal pipe pluggage and/or burner overheating.
8. Inadequate warm up of the pulverizer prior to feeding coal is hazardous since moist coal may plate out on the “cold” internals of the pulverizer and fuel piping. This increases the potential for a fire in the milling system.
9. Inadequate cool down of pulverizer prior to shutting off coal flow is hazardous since temperatures may exceed a safe limit for the remaining coal/air mixture. This increases the likelihood of a pulverizer or coal pipe fire/puff to occur.
10. Operating a pulverizer with too high an output fineness is considered less then optimal as increased fineness results in lower pulverizer capacity and higher pulverizer motor power consumption. In some cases, excessively high fineness may result in unusually high mill vibration.
11. Operating a pulverizer with too low an output fineness is considered less then optimal as low pulverized coal fineness will adversely affect furnace operation.
12. Operating a pulverizer with suspected or obvious mechanical problems with items such as a journal, spring assembly, scraper assembly, gear box, classifier, etc. should be avoided due to the potential of extensive mechanical damage and potentially hazardous operating conditions.
RELATED SEARCHES: